A common depiction of CNC machining, most times, involves working with a metallic workpiece. However, not only is CNC machining widely applicable to plastics, but plastic CNC machining is also one of the common machining processes in several industries.
The acceptance of plastic machining as a manufacturing process is due to the wide array of plastic CNC materials available. Furthermore, with the introduction of computer numerical control, the process becomes more accurate, faster, and suitable for making parts with tight tolerance. How much do you know about plastic CNC machining? This article discusses the materials compatible with the process, available techniques, and other things that can help your project.
Plastics for CNC Machining
Many machinable plastics are suitable for manufacturing parts and products several industries manufacture. Their use depends on their properties, with some machinable plastics, such as nylon, having excellent mechanical properties that allow them to replace metals. Below are the most common plastics for custom plastic machining:
ABS:
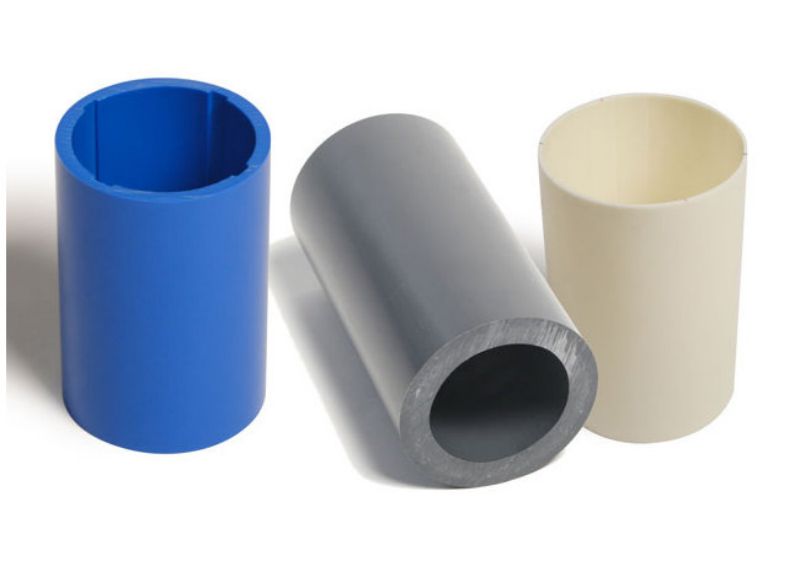
Acrylonitrile Butadiene Styrene, or ABS, is a lightweight CNC material known for its impact resistance, strength, and high machinability. Although it boasts good mechanical properties, its low chemical stability is evident in its susceptibility to greases, alcohols, and other chemical solvents. Also, the thermal stability of pure ABS (i.e., ABS without additives) is low, as the plastic polymer will burn even after removing the flame.
Pros
It is lightweight without losing its mechanical strength.
The plastic polymer is highly machinable, making it a highly popular rapid prototyping material.
ABS has a low melting point suitable (this is important for other rapid prototyping processes such as 3D printing and injection molding).
It has a high tensile strength.
ABS has high durability, which means a longer lifespan.
It is affordable.
Cons
It releases hot plastic fumes when subjected to heat.
You need proper ventilation to prevent the buildup of such gases.
It has a low melting point which can cause deformation from heat generated by the CNC machine.
Applications
ABS is a very popular engineering thermoplastics used by many rapid prototyping services in making products due to its excellent properties and affordability. It is applicable in the electrical and automotive industries in making parts such as keyboard caps, electronic enclosures, and car dashboard components.
Nylon
Nylon or polyamide is a low-friction plastic polymer with high impact, chemical, and abrasion resistance. Its excellent mechanical properties, such as strength (76mPa), durability, and hardness (116R), make it highly suitable for CNC machining and further improve its application in the automotive and medical part manufacturing industries.
Pros
Excellent mechanical properties.
It has a high tensile strength.
Cost-effective.
It is a lightweight polymer.
It is heat and chemical resistant.
Cons
It has low dimensional stability.
Nylon can take in moisture easily.
It is susceptible to strong mineral acids.
Applications
Nylon is a high-performing engineering thermoplastic applicable to prototyping and manufacturing real parts in the medical and automotive industries. Component manufactured from the CNC material includes bearings, washers, and tubes.
Acrylic
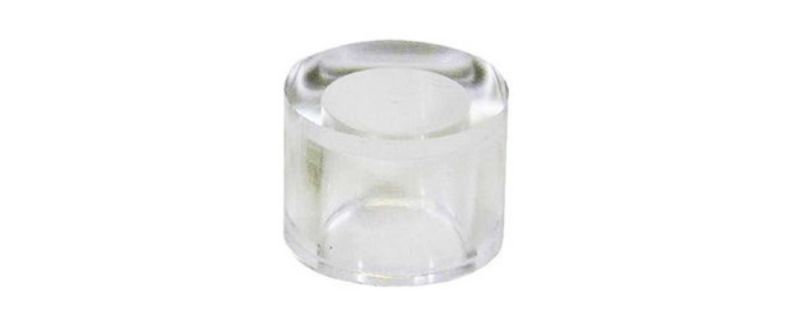
Acrylic or PMMA (Poly Methyl Methacrylate) is popular in plastic CNC machining due to its optical properties. The plastic polymer is translucence and scratch resistant, hence its applications in industries that require such properties. Aside from that, it has very good mechanical properties, evident in its toughness and impact resistance. With its cheapness, acrylic CNC machining has become an alternative to plastic polymers such as polycarbonate and glass.
Pros
It is lightweight.
Acrylic is highly chemical and UV resistant.
It has high machinability.
Acrylic has high chemical resistance.
Cons
It is not that resistant to heat, impact, and abrasion.
It can crack under heavy load.
It is not resistant to chlorinated/aromatic organic substances.
Applications
Acrylic is applicable in replacing materials such as polycarbonate and glass. As a result, it is applicable in the automotive industry for making light pipes and car indicator light covers and in other industries for making solar panels, greenhouse canopies, etc.
POM
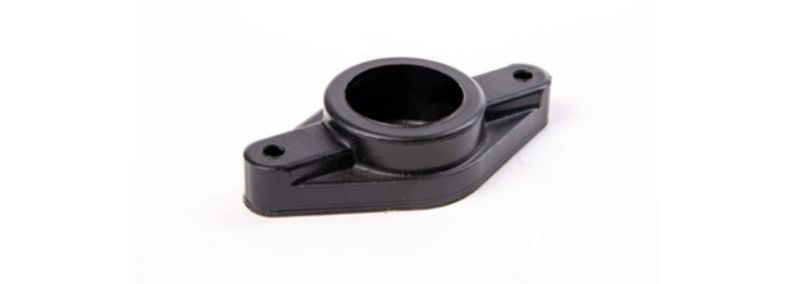
POM or Delrin (commercial name) is a highly machinable CNC plastic material chosen by many CNC machining services for its high strength and resistance to heat, chemicals, and wear/tear. There are several grades of Delrin, but most industries rely on the Delrin 150 and 570 as they are dimensionally stable.
Pros
They are the most machinable of all CNC plastic materials.
They have excellent chemical resistance.
They have high dimensional stability.
It has high tensile strength and durability, ensuring a longer lifespan.
Cons
It has poor resistance to acids.
Applications
POM finds its application across various industries. For instance, in the automotive sector, it is utilized to manufacture seat belt components. The medical equipment industry employs it to produce insulin pens, while the consumer goods sector makes use of POM to fabricate electronic cigarettes and water meters.
HDPE
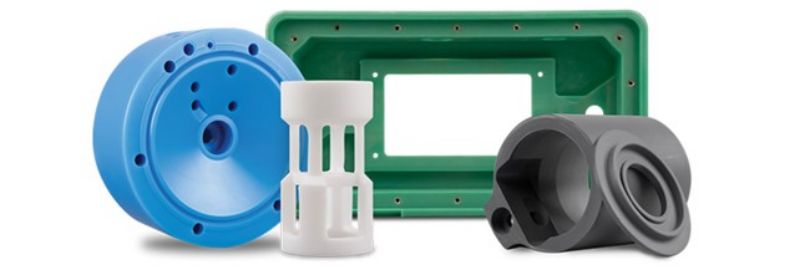
High-density polyethylene plastic is a thermoplastic with high resistance to stress and corrosive chemicals. It offers excellent mechanical properties such as tensile strength (4000PSI) and hardness (R65) than its counterpart, the LDPE replacing it in applications with such requirements.
Pros
It is a flexible machinable plastic.
It is highly resistant to stress and chemicals.
It has excellent mechanical properties.
ABS has high durability, which means a longer lifespan.
Cons
It has poor UV resistance.
Applications
HDPE It has a variety of applications, including prototyping, creating gears, bearings, packaging, electrical insulation, and medical equipment. It is ideal for prototyping as it can be machined quickly and easily, and its low cost makes it great for creating multiple iterations. Besides, it’s a good material for gears due to its low coefficient of friction and high wear resistance, and for bearings, because it’s self-lubricating and chemically resistant.
LDPE
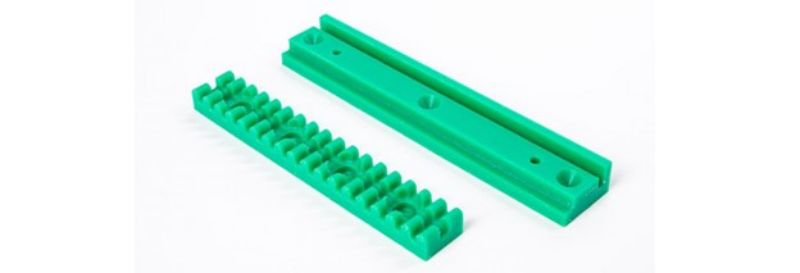
LDPE is a tough, flexible plastic polymer with good chemical resistance and low temperature. It is widely applicable in the medical part manufacturing industry for making prosthetics and orthotics.
Pros
It is tough and flexible.
It is highly corrosion-resistant.
It is easy to seal using heat techniques such as welding.
Cons
It is unsuitable for parts that require high-temperature resistance.
It has low stiffness and structural strength.
Applications
LDPE is often used for producing custom gears and mechanical components, electrical components like insulators and housings for electronic devices, and parts with a polished or glossy appearance. What’s more. its low coefficient of friction, high insulation resistance, and durability make it an ideal material for high-performance applications.
Polycarbonate
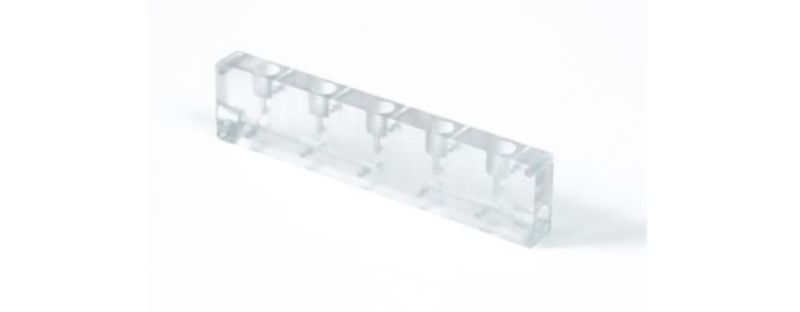
PC is a tough but lightweight plastic polymer with heat retardant and electrical insulating properties. Like acrylic, it can replace glass due to its natural transparency.
Pros
It is more efficient than most engineering thermoplastics.
It is naturally transparent and can transmit light.
It takes on color very well.
It has high tensile strength and durability.
PC is resistant to diluted acids, oils, and greases.
Cons
It degrades after prolonged exposure to water over 60°C.
It is susceptible to hydrocarbon wear.
It will yellow over time after prolonged exposure to UV rays.
Applications
Based on its light properties, polycarbonate can replace glass material. Hence, it is used in making safety goggles and CDs/DVDs. Aside from that, it is suitable for making surgical implements and circuit breakers.
Plastic CNC Machining Methods
CNC plastic part machining involves using a computer-controlled machine to remove part of the plastic polymer to form the desired product. The subtractive manufacturing process can create myriads of parts with tight tolerance, uniformity, and accuracy using the following methods.
CNC Turning
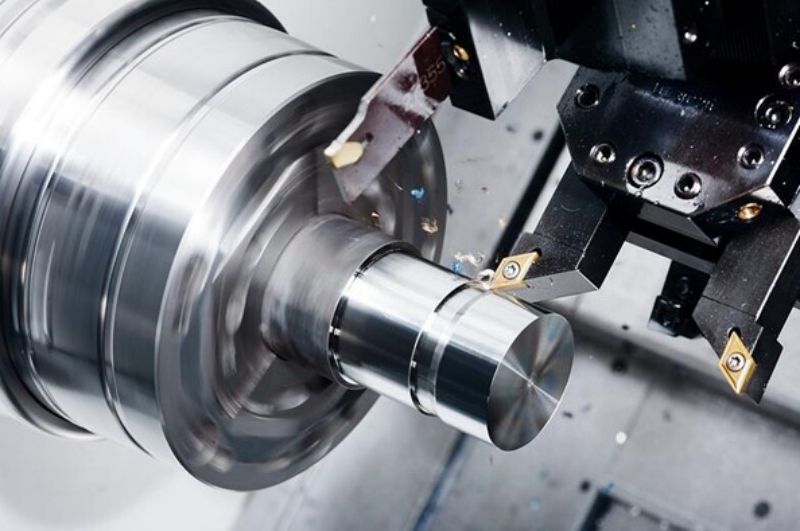
CNC turning is a machining technique that involves holding the workpiece on a lathe and rotating it against the cutting tool by spinning or turning. There are also several types of CNC turning, including:
Straight or cylindrical CNC turning is suitable for large cuts.
Taper CNC turning is suitable for creating parts with cone-like shapes.
There are several guidelines you can make use of in plastic CNC turning, including:
Ensure the cutting edges have a negative back rake to minimize rubbing.
Cutting edges should have a great relief angle.
Polish the workpiece surface for a better surface finish and reduced material buildup.
Reduce the feed rate to improve the precision of the final cuts (use a feed rate of 0.015 IPR for rough cuts and 0.005 IPR for precise cuts).
Tailor the clearance, side, and rake angles to the plastic material.
CNC Milling
CNC milling involves using a milling cutter to remove material from the workpiece to get the required part. There are different CNC milling machines divided into 3-axis mills and multi-axis mills.
On the one hand, a 3-axis CNC milling machine can move in three linear axes (left to right, back and forth, up and down). As a result, it is well suited for creating parts with simple designs. On the other hand, multi-axis mills can move in more than three axes. As a result, it is suitable for CNC machining plastic parts with complicated geometries.
There are several guidelines you can make use of in plastic CNC milling, including:
Machine a thermoplastic reinforced with carbon or glass with carbon tooling.
Increase the spindle speed by using clamps.
Reduce stress concentration by creating rounded internal corners.
Cooling directly on the router to disperse heat.
Choose rotational speed.
Debur plastic parts after the milling to improve the surface finishing.
CNC Drilling
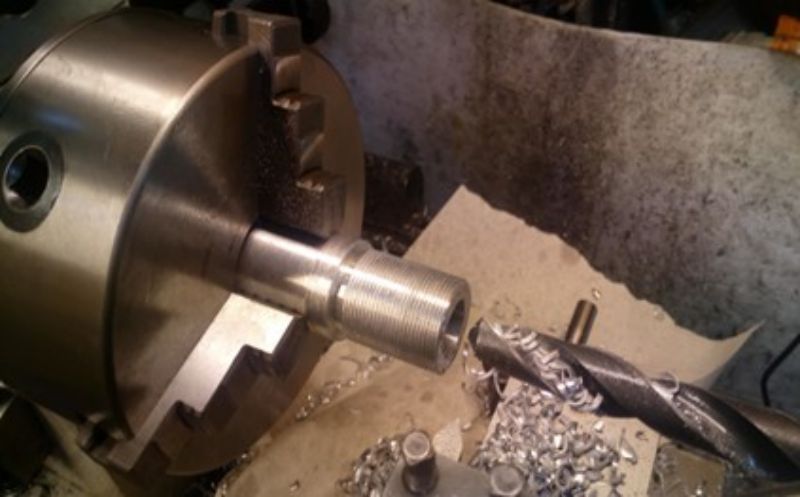
Plastic CNC drilling involves creating a hole in a plastic workpiece using a drill mounted with a drill bit. The drill bit’s size and shape determine the hole’s size. Furthermore, it also plays a role in chip evacuation. The types of drill press you can use include bench, upright, and radial.
There are several guidelines you can make use of in plastic CNC drilling, including:
Ensure you use sharp CNC drill bits to avoid putting stress on the plastic workpiece.
Use the right drill bit. For example, a 90 to 118° drill bit with a 9 to 15° lip angle is suitable for most thermoplastic (for acrylic, use a 0° rake).
Ensure an easy chip ejection by choosing the right drill bit.
Use a cooling system to alleviate more generated during the machining process.
To remove the CNC drill without damage, ensure the drilling depth is less than three or four times. the drill diameter. Also, reduce the feed rate when the drill has almost exited the material.
Alternatives to Plastic Machining
Aside from CNC plastic part machining, other rapid prototyping processes can serve as alternatives. Common ones include:
Injection Molding
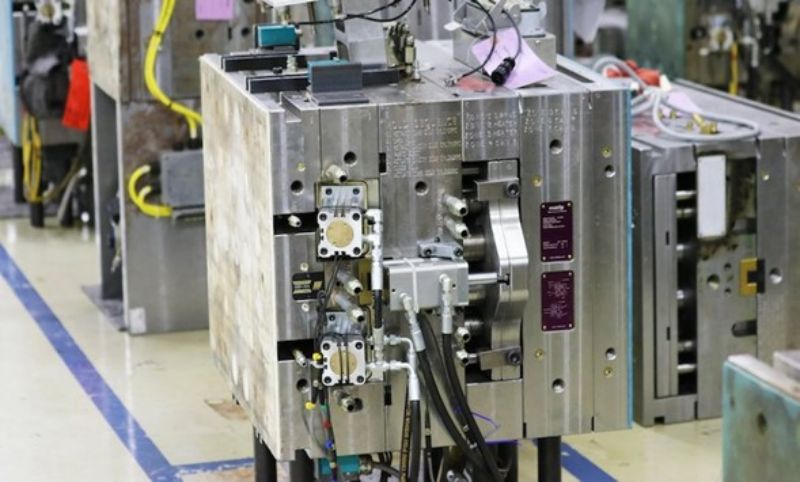
This is a popular mass-production process for working with plastic workpieces. Injection molding involves creating a mold from aluminum or steel depending on factors such as longevity. Afterward, molten plastic is injected into the mold cavity, cools, and forms the desired shape.
Plastic injection molding is suitable for both prototyping and manufacturing of real parts. Aside from that, it is a cost-effective method suitable for parts with complex and simple designs. Furthermore, injection molded parts hardly require additional work or surface treatment.
3D Printing
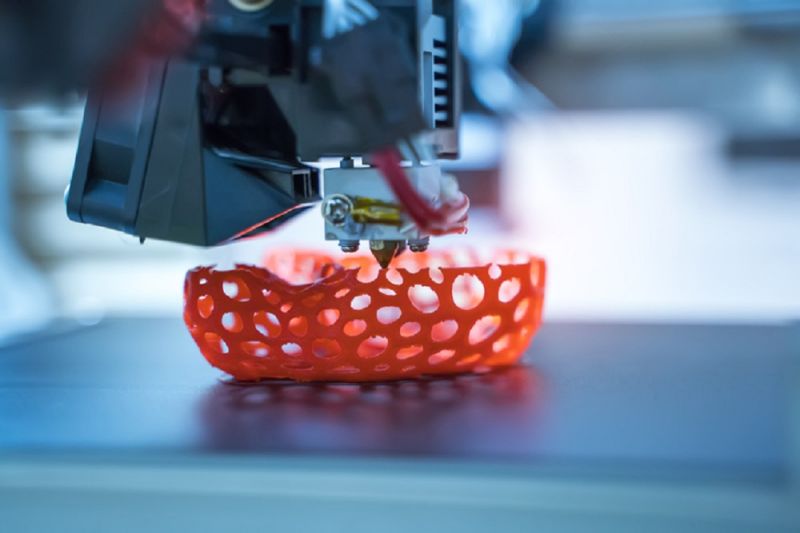
3D printing is the most common prototyping method used in small-scale businesses. The additive manufacturing process is a rapid prototyping tool comprising technologies such as Stereolithography (SLA), Fused Deposition Modeling (FDM), and Selective Laser Sintering (SLS) used for working on thermoplastics such as nylon, PLA, ABS, and ULTEM.
Each technology involves creating 3D digital models and building the desired parts layer by layer. This is like plastic CNC machining, although it incurs lesser material wastage, unlike the latter. Furthermore, it eliminates the need for tooling and is more suitable for making parts with complex designs.
Vacuum Casting
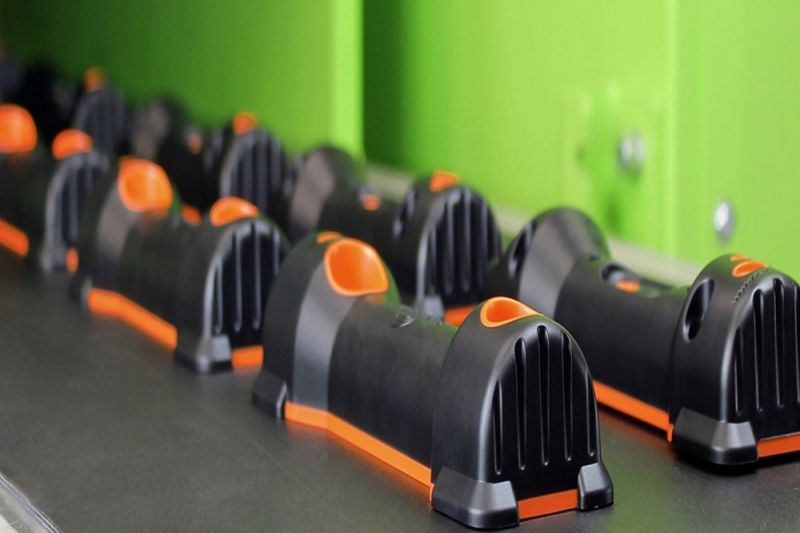
Vacuum casting or polyurethane/urethane casting involves silicon molds and resins to make a copy of a master pattern. The rapid prototyping process is suitable for creating plastic with high quality. Furthermore, the copies are applicable in visualizing ideas or troubleshooting design flaws.
Industrial Applications of Plastic CNC Machining
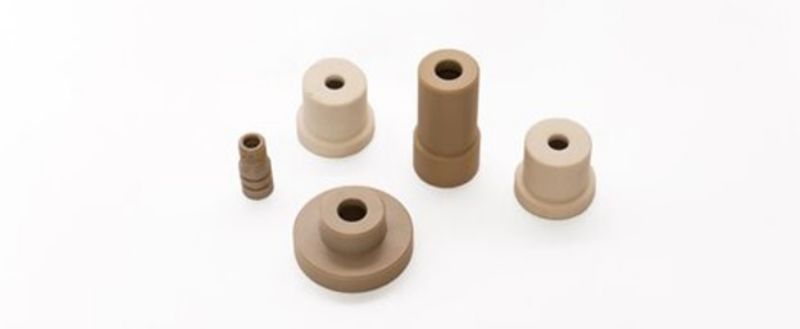
Plastic CNC machining is widely applicable due to benefits such as accuracy, precision, and tight tolerance. Common industrial applications of the process include:
Medical Industry
CNC plastic machining is currently applicable in manufacturing medical machined parts such as prosthetic limbs and artificial hearts. Its high degree of accuracy and repeatability allows it to meet the stringent safety standards required by the industry. Furthermore, there is a myriad of material options, and it produces complex shapes.
Automotive Components
Both car designers and engineers use Plastic CNC machining to make real-time automotive components and prototypes. Plastic is widely applicable in the industry in making custom cnc plastic parts such as dashboards due to its lightweight, which reduces fuel consumption. Furthermore, plastic is resistant to corrosion and wear, which most automotive components experience. Aside from that, plastic is moldable into complex shapes easily.
Aerospace Parts
Aerospace part manufacturing requires a manufacturing method that has high precision and tight tolerances. As a result, the industry opts for CNC machining in designing, testing, and building different aerospace machined parts. Plastic materials are applicable due to their suitability for complex shapes, strength, lightweight and high chemicals, and heat resistance.
Electronic Industry
The electronic industry also favors CNC plastic machining due to its high precision and repeatability. Currently, the process is used for making CNC-machined plastic electronic parts such as wire enclosures, device keypads, and LCD screens.
When to Choose Plastic CNC Machining
Choosing from the many plastic manufacturing processes discussed above can be challenging. As a result, below is a few consideration that can help you decide if plastic CNC machining is the better process for your project:
If Plastic Prototype Design with Tight Tolerance
CNC plastic machining is the better method for making parts with designs requiring tight tolerances. A conventional CNC milling machine can achieve a tight tolerance of about 4 μm.
If Plastic Prototype Requires Quality Surface Finish
CNC machine offers a high-quality surface finish making it suitable if your project does not need an additional surface finishing process. This is unlike 3D printing, which leaves layer marks during printing.
If Plastic Prototype Requires Special Materials
Plastic CNC machining can be used to produce parts from a wide range of plastic materials, including those with special properties such as high-temperature resistance, high strength, or high chemical resistance. This makes it an ideal choice for creating prototypes with specialized requirements.
If Your Products Are in Testing Stage
CNC machining relies on 3D models, which are easy to change. Since the testing stage requires constant modification, CNC machining allows designers and manufacturers to create functional plastic prototypes to test and troubleshoot design flaws.
· If You Need an Economical Option
Like other manufacturing methods, plastic CNC machining is suitable for making parts cost-effectively. Plastics are less costly than metals and other materials, such as composites. Furthermore, computer numerical control is more accurate, and the process is suitable for complex design.
Conclusion
CNC plastic machining is a widely accepted process industrially due to its accuracy, speed, and suitability for making parts with tight tolerance. This article talks about the different CNC machining materials compatible with the process, available techniques, and other things that can help your project.
Choosing the right machining technique can be very challenging, necessitating you to outsource to a plastic CNC service provider. At GuanSheng we offer custom plastic CNC machining services and can help you make different parts for prototyping or real-time use based on your requirements.
We have several plastic materials suitable for CNC machining with a stringent and streamlined selection process. Furthermore, our engineering team can provide professional material selection advice and design suggestion. Upload your design today and get instant quotes and free DfM analysis at a competitive price.
Post time: Nov-13-2023